BLANCPAIN, the originator of modern mechanical diving watches, has injected new vitality into the Fifty Fathoms series with its latest 42mm automatic diving watch in red gold and titanium alloy models. It continues to enrich the classic Fifty Fathoms family masterpieces. The titanium alloy watch uses grade 23 titanium alloy, which achieves a clever balance of lightness and strength.
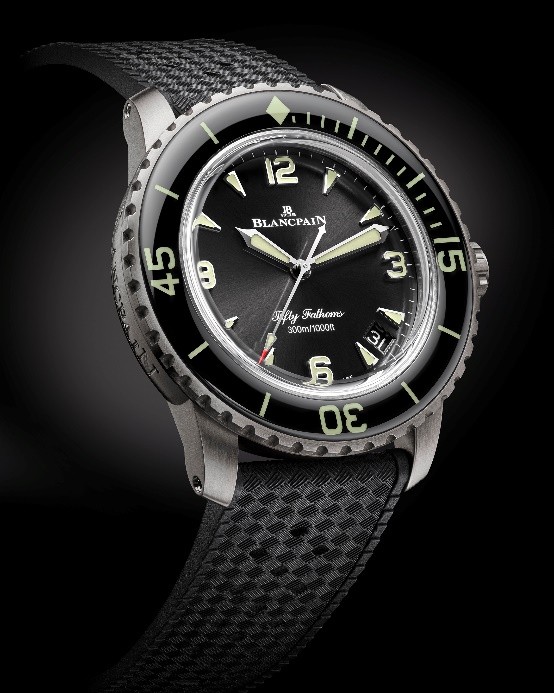
Fifty Fathoms classic watch 42mm diameter titanium alloy new model 5010
Grade 23 titanium alloy: super light, super strong, super hypoallergenic
In the watchmaking process of Blancpain’s Habillage workshop (Blancpain’s case-making workshop), patience and gentleness are the first rules when dealing with titanium. If this rule is violated, even though titanium has exceptionally high strength and excellent durability, it may explode and catch fire in just a fraction of a second during processing.
Titanium is more robust than mild steel but 45% lighter. In addition, titanium has extraordinary corrosion resistance. It is resistant to salt water and maintains its bright silver color for a long time. Finally, titanium does not cause allergic reactions, essential for applications that come into contact with the skin. For those who want a combination of high strength, lightweight, corrosion resistance, extreme toughness, and wear resistance, titanium is the material of choice. In short, it has all the features and advantages required for a sports watch.
Although using titanium to make watch cases and bracelets and applying it to the external parts of the watch is a compelling use case, Blancpain’s first application of titanium was to make the watch’s interior. Movement parts. In 2006, Blancpain’s first new-generation movement—the 13R0 eight-day power reserve manual winding movement—debuted. At that time, the brand chose titanium to build the balance wheel. Titanium’s light weight reduces energy consumption, helping to achieve the watch’s long power reserve goals.
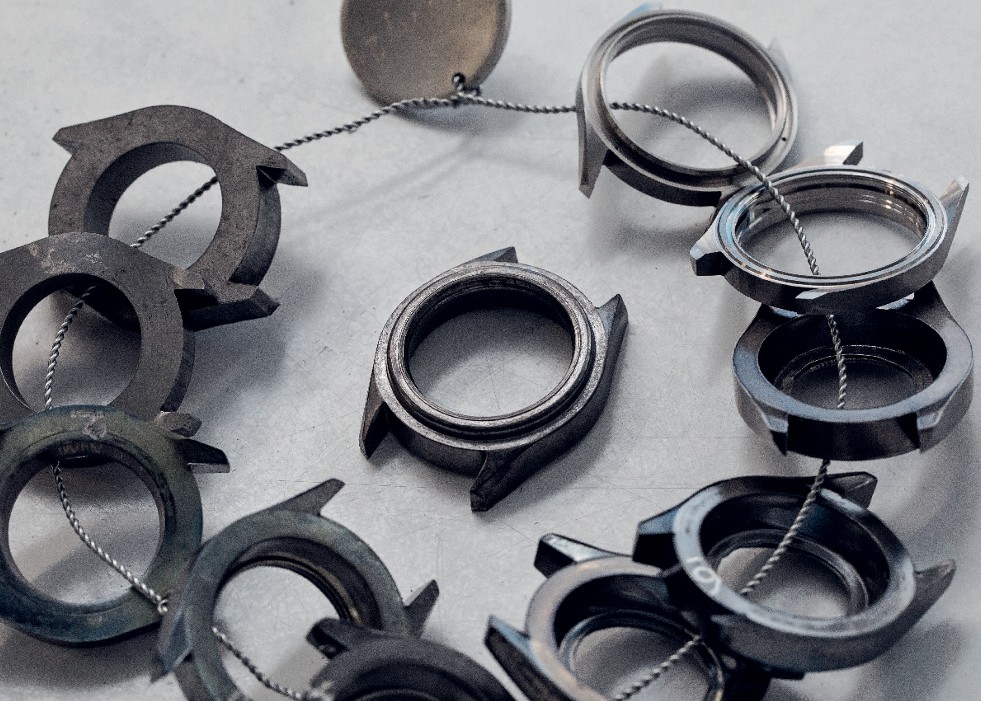
A series of production processes for the Fifty Fathoms Bathyscaphe watch case
Then, it’s time to create the second step in using titanium in watchmaking – a titanium case and bracelet. However, producing titanium watches involves more than simply making components out of pure titanium. Pure titanium is not an ideal material for making timepieces. Instead, its properties are enhanced by adding small amounts of aluminum (6%) and vanadium (4%). This alloy is often referred to as grade 5 titanium alloy. Some people also refer to grade 5 titanium alloy as “medical grade” titanium alloy because it is a good choice for medical devices such as artificial joints. Beyond the standard of Grade 5 titanium alloys, there is a variant called Grade 23 titanium alloys or extremely small interstitial titanium alloys (“ELI”). It differs from grade 5 titanium in purity: grade 23 titanium is purer due to reduced oxygen content. To meet the standards of grade 23 titanium alloy, the oxygen content in the alloy must not exceed 0.13%. Reducing the oxygen content increases the toughness of the metal. Grade 23 titanium alloy has become a material of choice due to its excellent strength, lightweight, corrosion resistance, and toughness. Best replica watches.
It is this performance improvement that has led Blancpain to use grade 23 titanium for eight watches launched in recent years, all from the brand’s sports series, including two Air Command chronographs (available in two different sizes) Optional, one with a case diameter of 42.5 mm and the other with a case diameter of 36 mm), three Fifty Fathoms Bathyscaphe watches (respectively: complete calendar moon phase watch, clock, and Self-winding watch), a Fifty Fathoms series tourbillon watch, a Fifty Fathoms series coelacanth technology Gombessa watch and the latest 2024 Fifty Fathoms series classic watch 42mm diameter 5010 titanium alloy model.
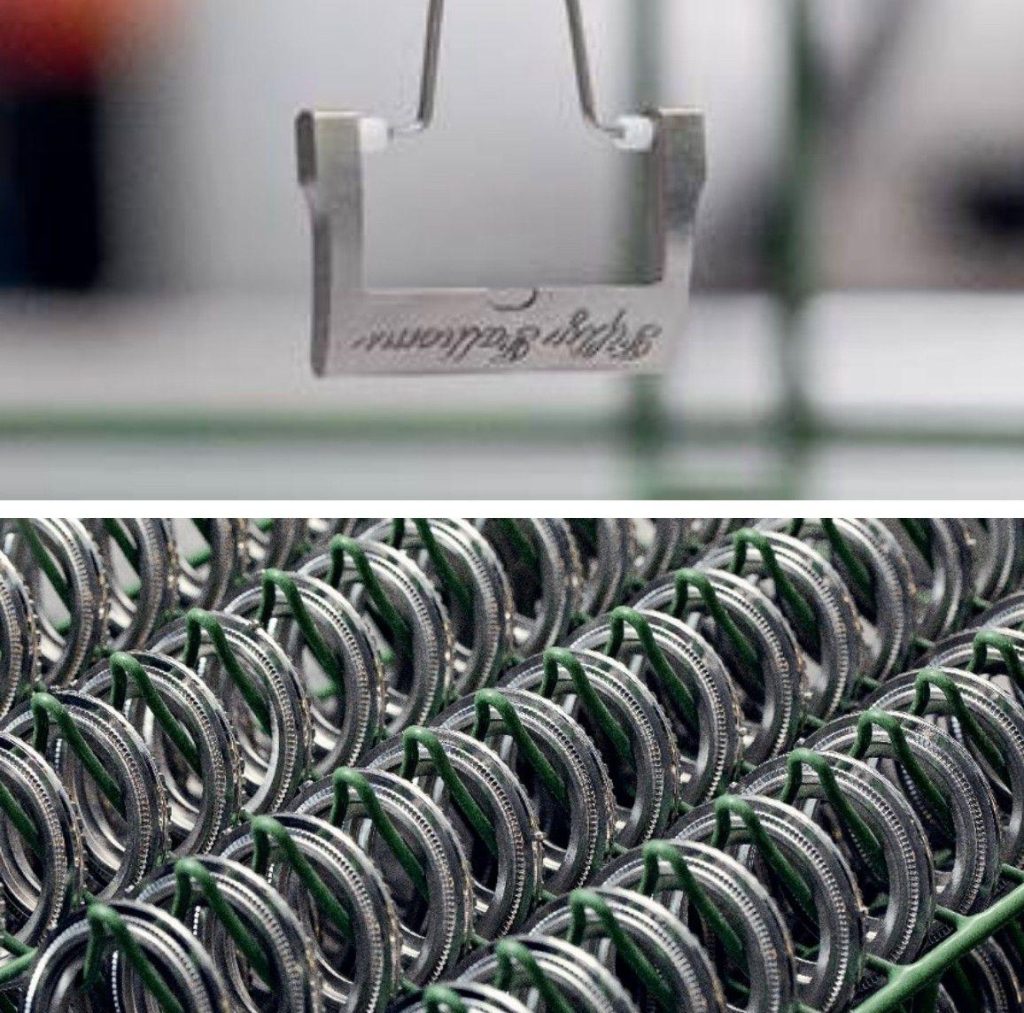
Titanium has many advantages but is also costly for watch cases or bracelets. The properties that make it so desirable in the final product, such as hardness and toughness, make it more difficult to machine and polish than steel or gold. Although the Blancpain factory that produces titanium watch cases is the same workshop that produces other metal watch cases/bracelets, the processes and tools used to produce titanium are different. According to the production process of titanium watch cases, watchmakers first stamp out the rough shape of the case and lug it from a titanium plate at high temperatures – the thickness of which is determined by the final thickness of the case. This process differs significantly from the initial steps in creating a steel or gold watch case. The production of stainless steel and gold parts will follow ancient methods, such as stamping at low temperatures. The process details of high-temperature stamping are strictly confidential industrial secrets, and the requirements for parameters are strict: temperature, air, cooling time, and stamping tools all play a vital role. Generally speaking, titanium plates need to be processed multiple times. The titanium metal must be cooled each time it is heated in certain air conditions. Metallurgists call this technique annealing, where the material is tempered. After completing these processes, the final product is a roughly formed watch case with attached lugs.

Machining of titanium: unique and demanding
Next, several processes must be applied to the titanium case back and bezel. These processes will process a long titanium rod into various parts. However, heating and cooling requirements still need to be retained to ensure processing quality. If the annealing process is omitted, the parts will be at risk of deformation.
In the following process, the Blancpain Habillage workshop’s requirements for exquisite skills are similar to the cutting/annealing process. The first stage of machining the watch case is called tournage (circular cutting). A rotating cutting head – which can also be thought of as a kind of “burin à plaquette” (technically known as a “burin à plaquette”), the shape of which is determined by the specific case original to be cut – is pressed against the surface of the watch. Turning it over in the tool on the shell is probably similar to the core-shell processing method used more than a hundred years ago. The first step in this process is to create the inner diameter of the case body, which will also become the reference standard for subsequent steps. Likewise, it is pretty similar to the turning process of a stainless steel or gold watch case. However, titanium has its unique requirements. The first is the cooling of the cutting tool. When turning other materials, watchmakers use oil slurries, but this method is not advisable for titanium because the cutting tools generate a lot of heat.
For this reason, watchmakers choose water-based emulsions for titanium. Even so, the risk of titanium fire and explosion still exists. Tools specifically designed for machining titanium are therefore equipped with high-performance flame detection and extinguishing safety systems. These systems can activate quickly in just one second to prevent fires.
Many machining steps are determined by the watch case’s design details, each of which is related to a specific original part of the case body and requires a uniquely shaped cutting workpiece. Every step in the process must adhere to stringent tolerance standards, which is valid for every Blancpain timepiece, but more importantly for diving watches (such as the Fifty Fathoms series watches and the Fifty Fathoms Deep The high degree of water resistance required for submersible Bathyscaphe watches). The key to correctly installing the case back, bezel, and seals is to ensure extremely high accuracy.
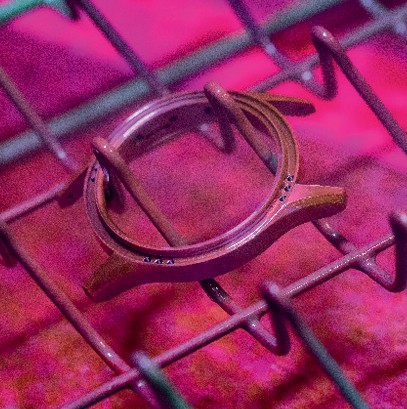
There are other steps to complete after that. An important step is drilling, which is necessary for the crown and the lugs that connect the strap. The Blancpain Air Command Chronograph has additional holes for its two chronograph pushers. Drilling is known as “réalisation des logements par fraisage” (creating mortises by drilling) and requires similar precision to turning. When performing this process, the same precautions and extraordinary measures are needed to prevent sudden fire or explosion.
Skilled masters always do polishing.
After completing multiple processes, such as turning and milling, it comes to fine grinding, metal engraving, and polishing. A classic example of pure hand-made watchmaking is using classic milled stones to create perfect, simple connection points between the lugs and the case body. This is all work that needs to be done on the inside and outside of the case, as the lugs have borders on the outside and inside. Not only does the watchmaker have to use a milling stone to create clean lines at the connection points, but they also have to be careful to maintain a flat, straight profile on the inner surface of the lugs. The milling stone is a grinding tool reminiscent of the watchmaking tradition, consisting of a rotating grinding stone. For watchmakers, it is very time-consuming and laborious to successfully create a clear and distinct connection point between the lugs and the curved surface of the case. Once the meticulous milling of the connection points between the case and lugs is completed, several additional steps of hand machining are performed. Next comes polishing, a process that must be done meticulously by hand to avoid damaging the lines that have been precisely milled between the lugs and the case.
Polishing, especially the process requiring complex shapes and textures, has always been the responsibility of skilled masters. The entire case surface of this Fifty Fathoms titanium model is brushed. The challenge for the polisher is to ensure that the filaments on the brushed surface remain consistent in density and line direction. Artisans must have very skilled skills when drawing the connection between the lugs and the case. The drawing process must not touch or interfere with the precise, distinct joints that were previously milled.
Blancpain’s two new Air Command titanium watches are undoubtedly another test of the skills of watchmakers. In both watches, the lugs’ top surface has polishing and brushing processes. The boundary line between the two grinding processes must be marked and positioned appropriately. This can only be achieved by placing a protective plastic film over one area while sanding the other.
Additional steps are required when creating the rotating bezel and case back. The rotating bezel is one of the leading technical features of diving and aviation fake watches. To facilitate the bezel’s rotation, some embossed patterns help the grip become an integral part of the design. This embossed pattern must be formed on the outside of the bezel since all bezels are inlaid with an inner ring decorated with bezel time scales (for example, the Fifty Fathoms Bathyscaphe watch and the Air Command watch use ceramic inner rings, the Fifty Fathoms series Tourbillon watches use a curved sapphire glass inner ring), which requires cutting a groove in the bezel for inlaying the inner ring. Artisans will use turning methods to form grooves inside the bezel. The tolerances of this machining process must be controlled very precisely because the ceramic inner ring or sapphire glass inner ring and the metal groove must fit tightly and perfectly. Finally, the back of the bezel of a dive watch has excellent, precisely positioned small ratchet teeth that form part of the bezel’s unidirectional rotation system. These ratchet teeth are stamped into the bezel.
Blancpain also equips all 23-grade titanium alloy watches in the Fifty Fathoms series with bracelets made of the same material. The design style is the iconic style that Blancpain commonly used in the 1990s. Watch connoisseurs will immediately recognize the signature features of the classic Blancpain 71 stainless steel bracelet, which is world-famous for its elegant design and comfort on the wrist.